Paul Revere, your name is magic. A piece of silver, an engraving, a midnight ride — they’ve all been burnished by your hand and the tongues of your acolytes. You may have helped to start a revolution, but your foundries were nothing short of revolutionary. Your industrial pursuits, one part patriotism, one part profiteering, are the stuff of legend. And one legend often begets another.
Enter the frigate Constitution and an order from the Treasury Department. In late 1794, the Treasury ordered a large number of drawn copper bolts from England for the new Federal frigates being built. Because copper bolts would not corrode like iron, these were essential for fastening timbers that might come into contact with seawater. They were also important for ships whose hulls were sheathed in copper. Iron bolts would have degraded even faster because of galvanic action, a chemical reaction brought on by the close proximity of the copper sheathing and the iron. The government had to order them from England because no one in America knew the secret of making tough, yet malleable copper bolts.
In a letter to Captain James Sever in Portsmouth, Secretary of War Henry Knox explained there had been a mistake in the bolt order: “Unfortunately, a mistake in copying the directions for the bolts at the Office of the Commissioners of the revenue last year, has occasioned the sending out the largest bolts of 1 7/8ths inches diameter instead of 1 & 3/8ths. Experiments have been made to reduce them. It is under consideration whether to reduce them or not. The bolts which have arrived here are of pure copper.”1
Welcome Paul Revere. He’d been running a furnace for seven years, casting bells for three years, and cannons for one year when Boston Navy Agent Henry Jackson asked if he could reduce the oversized copper bolts received from England. According to Revere, “I then found out that it was necessary that bolts and spikes for ship building should be made out of malleable copper. After discoursing with a number of old coppersmiths, they one and all agreed that they could not melt copper and make it malleable as to hammer it hot. I farther found that it was a secret in Europe that lay in but a very few breasts”2
Undeterred, Revere began a series of “trials” to discover the secret. Melting and casting copper in molds made the finished product brittle. Cold working, the process of striking cold copper with a hammer to shape it, also produced a hard but brittle bolt. Heating the metal, a process called annealing, rearranged the metal’s atomic structure to make it more ductile and tough. At last he combined these processes and discovered the secret of the European smiths: “Skilled coppersmiths fabricated malleable copper by a combination of hot- and cold-working processes, alternately heating, cooling, and hammering the copper until producing the desired blend of qualities. In this manner, copper could become both hard and tough, or in other words, simultaneously resistant to penetration, resistant to breaking, and non-brittle.”3 These properties were essential for copper bolts that had to be driven through many feet of hard live oak.
The actual process of drawing down the ship’s bolts was not recorded, but in a 1796 letter, Revere provided a clue to the technique. It appears the bolts were reduced by being beaten with a trip hammer into a swage, a sort of die used to shape metal in traditional blacksmithing. He must have done this several times, once while the metal was hot and again when it was cold.4
Revere finished resizing 15 tons of copper bolts in October 1795 and submitted a bill for $2,756.5 Three months later, Secretary of War Timothy Pickering sent an emphatic letter to Henry Jackson: “If this work is still going on, pray let it be immediately stopped. There is danger of spoiling the temper of the bolts. It is monstrously expensive, and not necessary. I shall write you more particularly about the manner in which the large bolts are to the be used: in the meantime I repeat let no more be reduced.”6
Pickering had no idea Revere had discovered the secret of making malleable copper bolts, so his alarm is understandable. In fact, Joshua Humphreys himself had declared “there was no person in America that could make copper malleable so that it could be drawn into bolts and spikes.”7 Humphreys later admitted his mistake, and became Revere’s warm friend.
This brings us back to Constitution’s bolts. Now that the over sized bolts had been reduced, Naval Constructor George Claghorn had questions about how to use them. The War Department wrote back (or rather, it transmitted Joshua Humphrey’s ideas about the matter) with the answer:
“As the Copper bolts have been reduced to 1 3/8 Inch diameter you are hereby directed to secure the Floor timbers with two of the 1 3/8 bolts in each Floor timber, one of which must be drove through the lower Keelson, and the other through the upper Keelson, both bolts are to go through the deadwood and Keel. The Cross Chocks are to be bolted with one bolt in each of 1 3/8 diameter which is to be drove through the lower Keelson, one of the lower Futtock heels and Keel. All the bolts are to be well clinched on rings let up into the Keel.”8
For those of us not well versed in the lingo of the shipwright, the following diagram might help to make these instructions a bit clearer.
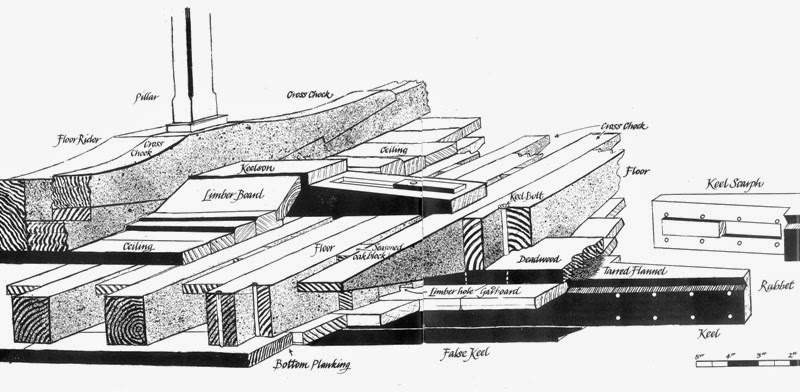
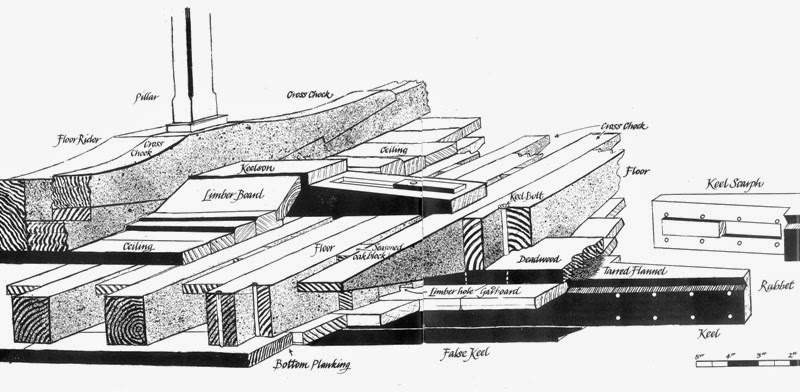
It just so happens that the Navy drew out a number of the 1 3/8 inch bolts from deep in Constitution’s hull during the 1990s restoration. They wanted to determine if the bolts were still sound, or if years of exposed to seawater and hull movement had degraded them. What they found when they examined them was that the combination of English copper and Revere’s reworking held up very well indeed. The Navy loaned one example to the Museum. It was cut in half lengthwise so scientists at MIT could perform tests on it. Its composition is almost pure copper, and it measures almost exactly 1 3/8 inch in diameter. The joints between the various pieces of timber may be clearly seen where the copper has wasted more than in other places.
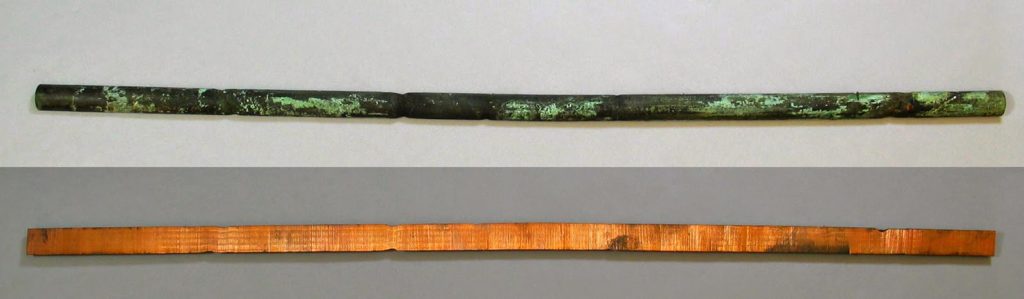
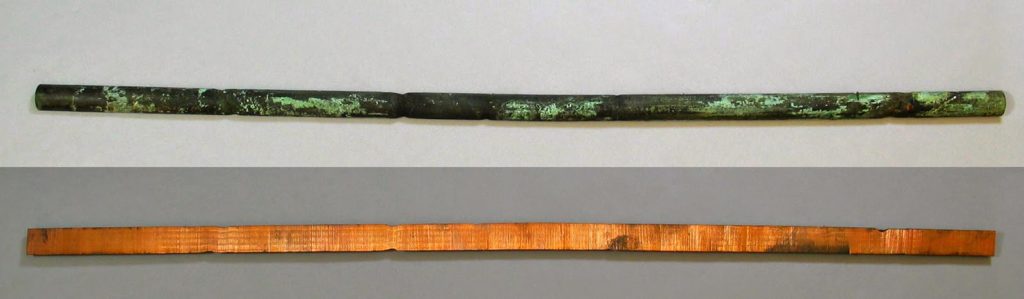
1 Sec. Henry Knox to James Sever 14 May 1795, accessed via https://wardepartmentpapers.org/.
2 Revere to Harrison Gray Otis, 11, March 1800, quoted in Robert Martello, Midnight Ride, Industrial Dawn: Paul Revere and the Growth of American Enterprise (Baltimore: John Hopkins University Press, 2010), 191.
3 Ibid., 193.
4 Ibid., 194.
5 Ibid., 197.
6 Timothy Pickering to Henry Jackson 27 Jan 1796, accessed via https://wardepartmentpapers.org/.
7 Revere to Harrison Gray Otis, 11, March 1800.
8 James McHenry to George Claghorne, 15 March 1796, accessed via https://wardepartmentpapers.org/.
The Author(s)
Matthew Brenckle
Research Historian, USS Constitution Museum
Matthew Brenckle was the Research Historian at the USS Constitution Museum from 2006 to 2016.