From Hemp and Flax may Canvas Sails
And Ropes be drawn, that seldom fails,
In stormy Winds, to act their Part,
If twisted well by human Art.
-Sotweed Redivivus, or the Planters Looking-Glass, 1730
In an age when ships moved only with the power of the wind, canvas for sails – the “engine” of every sailing ship- became an important strategic asset. Preserving and growing a stock of timber suitable for shipbuilding weighed heavily on the minds of most naval bureaucracies in the 18th and 19th centuries, but finding a steady supply of sail canvas for warships came in a close second.
Canvas weavers in this period made their products from hemp or flax yarns. Farmers in Northern Europe and along the Baltic grew vast quantities of both crops and processed them into clean, smooth fibers suitable for spinning into yarn (the weaver’s term for the threads that make up a piece of cloth). While the English word “canvas” comes from the Latin “cannabis,” or hemp, flax seems to have been the fiber of choice for most sails.
A huge amount of canvas came from Russia and Silesia (a region of central Europe now part of Poland, Germany, and the Czech Republic), where hemp cultivation had been carried on for centuries. Most sailors in the early 19th century thought flax canvas woven in the English towns of Bridport and Crewkerne was second only to Dutch canvas in strength and durability.
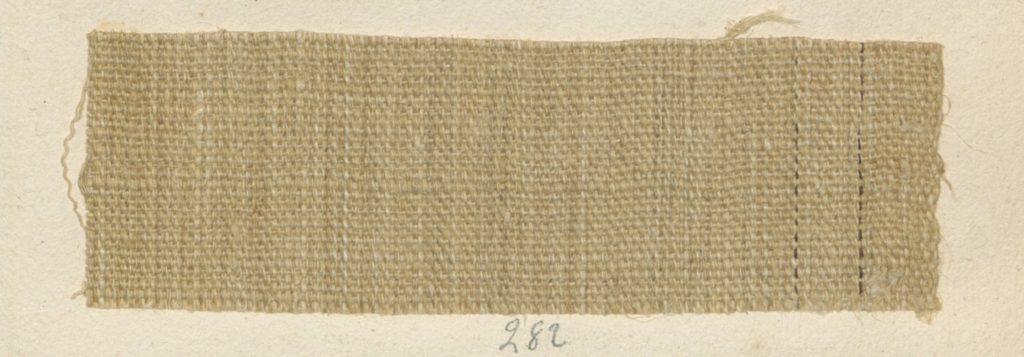
In America, small scale hemp and flax cultivation had been carried on since Europeans first colonized the region, but most sail canvas used in the ever-growing merchant fleet was imported from Europe. In the late 1780s, a number of enterprising Americans attempted to establish factories to make this valuable commodity from domestic flax and hemp.
One of the first companies of this sort was the Boston Duck Manufactory (sometimes referred to as the Sail Cloth Manufactory at Boston). Its establishment in Frog Lane consisted of “a lot of Land on which are 1 Spinning Shed, 180 by 16 feet, 1 d[itt]o 184 by 24; 1 Store, 60 by 28; and 3 Small Shops.” The company employed “about 200 Women & Girls together with about 50 Men.”
In 1790, when the government first contemplated building warships, the Manufactory’s agent Samuel Breck addressed a long letter to Secretary of War Henry Knox explaining the capabilities and benefits of the company:
“In this town is established a Sail Cloth manufactory on a very extensive Scale, the intention in promoting this object is to give employment to the Poor & to render our Country less dependent on Foreigners for that Article in whose power it was, by withholding their Canvass or if intercepted, to prevent the Sailing of our Ships. The establishment of this Factory will cost between thirty and forty thousand Dollars & as I [word crossed out] more than one third of the whole it becomes an object of consideration, no pecuniary influence however operates on this occasion as the sailcloth meets a ready sale both here & in the Southern States, but a wish that our State Ships, like those of other nations, should be clothed with our own manufacture. The quality, by the enclosed Certificates you will find highly approved, indeed it is universally allowed to be superior to any foreign Duck whatever.* This I impute to the particular quality of our Flax & the manner of manufacturing it. Our Director is an Englishman who carried on this branch of business for more than thirty years on a very extensive scale, & is not only a worthy man, but a thorough master of the business. At present about sixteen hundred yards of cloth is the average for each week altho’ two thousand has been made, but the great consumption of Flax has rendered it scarce & dear. The season, however is fast approaching when the produce of this year will come to market, and as it has been a plentiful one we flatter ourselves the works will be extended during the next year to four thousand yards a week, if so, our poor Citizens will be happily provided for.”
Despite promising beginnings, the factory was only profitable thanks to a bounty given by the state of Massachusetts for every bolt of canvas produced. That bounty expired in 1792 and from then on the fortunes of the Boston Duck Manufactory began to decline. Nevertheless, when the government decided to build its six frigates in 1794, much of the canvas used for both Constitution and at least two others came from the company. The first batch of canvas was delivered in December 1794, and in 1795 the company received another contract. By 1796, however, the company no longer remained viable and the land on which the factory stood was sold to proprietor Samuel Breck.
One of the earliest surviving US Navy contracts for sail cloth was made with Levi Shepherd and Sons of Northampton, MA in January 1800. According to the contract, Shepherd agreed to provide 400 bolts or “pieces” of canvas. Each bolt had to contain 36 yards of 24-inch-wide cloth. A bolt weighing 32 pounds cost the government $14.50, and 25 cents for each additional pound.
The Navy has a long history of requiring superior goods from its suppliers, and this canvas was no exception. The contract with Shepherd carefully spelled out exactly how he had to weave the cloth: “the said sail cloth is to be made of the best materials…the warp and filling are to be wholly of good hackelled flax and no part of tow, and…there is to be no sizing used in the manufacture of the cloth.”
Shepherd’s canvas must have proved satisfactory, because he received at least two more contracts through 1801, for a total of 51,400 yards of sail cloth. This may seem like a vast amount at first glance, but when we consider Constitution’s foretopsail alone required 23 bolts of canvas (828 yards), and her entire suit of sails required about 350 bolts (12,600 yards), Shepherd’s contract provided enough canvas for only about four suits of sails.
For more on the evolving nature of sail canvas and Constitution‘s sails in the 20th and 21st centuries, be sure to read next week’s Restoring an Icon blog post.
*Not everyone was a fan. In a letter to Navy Agent William Pennock, Josiah Fox said, “If the Bridport Pattent Canvas such as is in the British navy could be obtained it would be preferable to every other kind, the Boston Canvas has been found on trial to stretch very considerably.”
The Author(s)
Matthew Brenckle
Research Historian, USS Constitution Museum
Matthew Brenckle was the Research Historian at the USS Constitution Museum from 2006 to 2016.